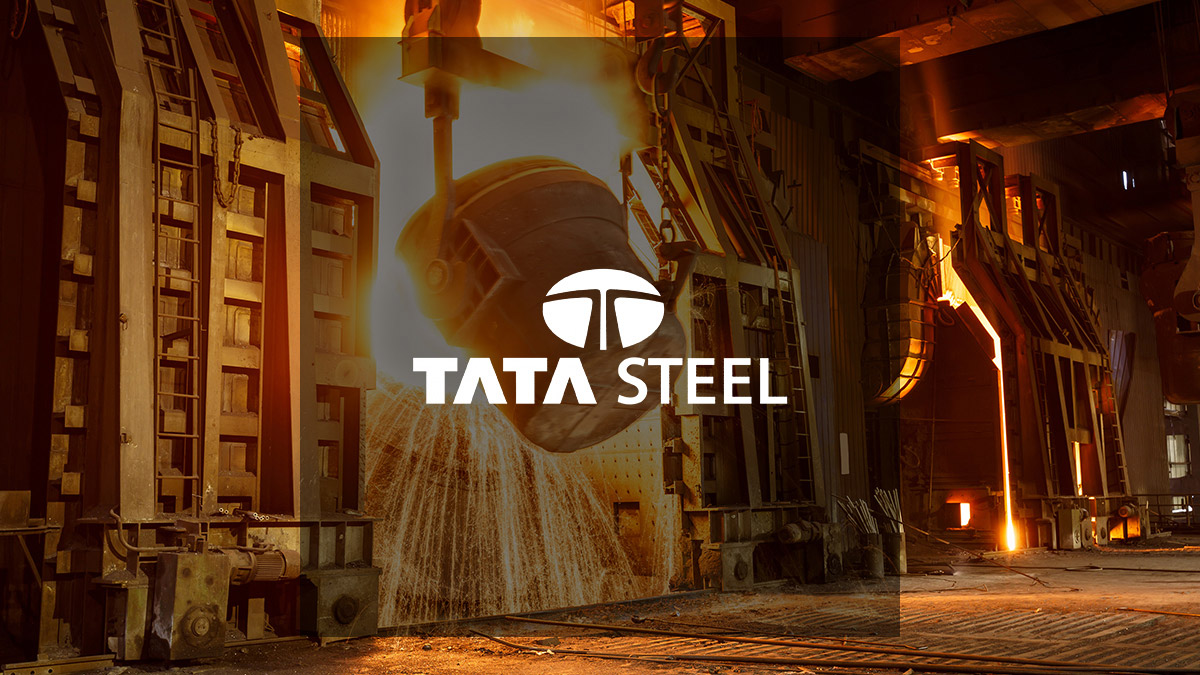
Steel giant Tata Steel enlisted the help of HVR Consulting Services Ltd to conduct a series of project and business risk assessments. The project risk assessments aimed to ensure all risks to the project were identified and analysed, and @RISK was used as the tool to analyse the project timescales.
Risk Management is the process of identifying, analysing and mitigating risk. This has often been conducted in a fairly haphazard way, with no real structure to the procedure. A more forward-looking approach was taken by the steel giant Tata Steel when they conducted a large-scale intermediate repair to the largest blast furnace in Europe, located at the Teesside Works at Redcar, England. The programme of work was high profile as the furnace is the only ironmaking unit for the whole Teesside Works. During the outage period all steel making and casting operations at Lackenby and ore sintering at the Redcar site ceased.
Tata Steel enlisted the help of HVR Consulting Services Ltd, recognised experts in the field of Risk Management, to conduct a series of project and business risk assessments. The project risk assessments aimed to ensure all risks to the project were identified and analysed, and @RISK was used as the tool to analyse the project timescales. Variability surrounding the duration of activities in the project plan was combined with risks from the Risk Register to create a risk model. This was then analysed using @RISK, not only to predict the likely project outcomes but also to identify key areas requiring management attention and opportunities for schedule saving.
The business assessments were conducted on the entire Commercial and Industrial (C&I) section of Tata Steel, to assess the impact of the blast furnace outage on the company. These business assessments again identified key risks to the Tata Steel business, encompassing commercial, financial, technical and logistical risks. A process model was designed using @RISK to model and forecast production throughput at the C&I business sites, incorporating the effect of the identified risks. This was then used to provide the blast furnace Steering Committee with guidance on steel stock build requirements, allowing commercial and production decisions to be made and tested.
The project was, within Tata Steel, heralded as a major success. The furnace reline was completed in a total outage of 68 days 9 hours, which was within the (extremely aggressive) 70-day window targeted. Each day of lost production would have cost Tata Steel a significant amount in lost production, so a minimal reline duration was paramount.
The key issue of slab stocking to feed the steel mills whilst the furnace was off line was also successful. The business operates with a set ‘irreducible minimum’ of stock, to cater for unforeseen fluctuations in furnace output, steel caster performance and in steel requirements. At the end of the outage the business had a slight surplus over the irreducible minimum, caused mainly by a downturn in orders for one of the mills during the outage period.
A subsequent ‘wash up’ meeting of the members of the furnace Steering Committee was held to identify the items which had been critical to the project’s success and to identify any lessons to be learned. The timescale risk analysis techniques (using @RISK) were considered to be a useful disciplined tool, giving some idea of the outage duration and dovetailing into the business risk assessment. The fact that the length of the outage duration was key to the success of the project meant that the schedule risk analysis was of immediate use as it helped the business plan for a realistic outage duration.
The business risk assessment, and in particular the @RISK process model, was seen as one of the critical success factors. The process model enabled the iron make levels prior to the furnace outage and the recommissioning rate to be realistically analysed, including the effects of the risks to the business and the uncertainty in the reline outage duration.