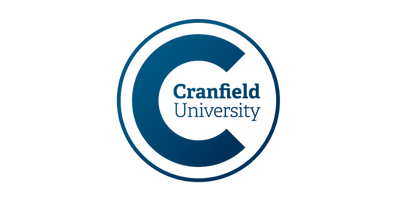
Cranfield University is a wholly postgraduate institution with a worldwide reputation for excellence and expertise in aerospace, automotive, defence, engineering, environment and water, health, management, and manufacturing. It is one of the top five research universities in the UK and combines academic study and qualifications with the commercial and business focus of industry.
Starting with Product Design and @RISK
A recent project focusing on sub-sea equipment for the oil and gas industry at Cranfield University provided evidence to business managers that a better return on investment (ROI) is achieved through enhancing a product's longterm reliability as a result of spending time and resources early in the product design lifecycle. The project is funded in part by the Engineering and Physical Sciences Research Council (EPSRC), the UK's main government agency for funding research and training in engineering and the physical sciences.
Cranfield's School of Applied Sciences uses @RISK software from Palisade to calculate the likelihood of sub-sea oil and gas production equipment failing, and the overall cost throughout the project life cycle, should it do so. @RISK is an Excel add-in using Monte Carlo simulation to show all potential scenarios, as well as the likelihood that each will occur, thereby providing the decision-maker with the most complete picture possible.
Sub-sea oil and gas equipment can be required to function in excess of 2000m below sea level. This means that the failure of any product, or product component, has huge ramifications. There are the practical considerations of difficult repair work, as well as the financial aspects. For example, the cost of a support vessel can exceed $200,000 per day, so depending on the severity of the malfunction and the length of time it takes to restore a system to working order, the total cost of intervention can be more than $10,000,000. In addition, for the duration of time that the equipment is out of service, oil or gas isn't being produced, which results in an opportunity cost.
@RISK Combines Risk Analysis Techniques
@RISK enables Cranfield to integrate the critical elements of the two core risk analysis techniques commonly used in the engineering field, RAM (Reliability, Availability, Maintainability) and Lifecycle Costing analysis (LCC). RAM focuses on the overall ability of an installation to perform its required functions over the period of time for which it was designed to be used. It does this by analysing the performance of each separate component of a system and combining the results to predict the total time for which the equipment will be available. Lifecycle Cost Analysis calculates the cost of a system over its entire life span, taking into account both the actual cost of repairing equipment, plus the lost revenue due to being unable to produce oil or gas during downtime.
Traditionally the disciplines are carried out in isolation, so it is difficult to obtain an accurate picture of the total cost of system downtime over its lifecycle. @RISK combines RAM and LCC inputs - as defined by the Cranfield project managers, into one model, and then runs thousands of simulations to show a distribution of all possible installation performance outcomes, the probability of each outcome occurring, and the lifecycle cost implications for each performance outcome.
Karl Woods
Engineering Doctorate Research Engineer, Cranfield University
@RISK Gives Confidence to Invest in Product Development
Karl Woods, Engineering Doctorate Research Engineer from Cranfield explains: “The 1970s saw a shift in thinking to consider the whole product life cycle and the realisation that it is beneficial to make things reliable over the longest time period that is possible and practical. However, this is often outweighed by companies' understandable reticence to spend money up-front on something that is as yet unproven and the outcome of which is uncertain. @RISK's sophisticated analysis enables us to measure the unknowns, and combine reliability forecasts with the cost of breakdowns, thereby illustrating that lack of investment in making a product more reliable can often be false economy in the longterm.”
The reliability of each component of a system can be converted into a distribution of 'time to failure' – that is the probability of how long it will take before requiring repair. These are all defined as input distributions for the @RISK model, which help calculate at what point in its lifecycle a product is more likely to fail.
@RISK provides end-users with a choice of outputs such as Net Present Value (NPV), Internal Rate of Return, Standard Technical Cost (the minimum selling price of oil required for the installation to be profitable), Lifecycle Cost and System availability, which they select depending on their needs. For example, using the distribution model that shows break even (the point at which the NPV of a project first becomes zero) is a useful measure of reliability – the more robust a system is, the sooner it could start to return a profit. One of @RISK's more useful features is its ability to generate graphical representations of what could happen rather than just providing an output of what is expected to happen (ie a mean value). As a result, companies can calculate accurately what level of investment in product design will provide them with the best ROI in the longterm.
@RISK Weighs Significance of Individual Components
Calculations are enhanced by @RISK's sensitivity analysis feature. This takes into account that the component in an overall system that is most sensitive in terms of reliability is not necessarily the most sensitive when it comes to cost.
For example, component A has a high failure rate, but is easy to maintain, so it does not cause huge problems if it stops working. On the other hand, component B, although more reliable, takes a long time to repair when it fails and therefore has a more adverse affect on the complete system and overall cost of downtime. Therefore overall, @RISK demonstrates that it is more beneficial to invest in making component B more robust.
Woods concludes: “The sensitivity analysis of @RISK means that we can weigh up the significance of failure for each element of a complex piece of equipment. End-users are therefore fully-informed and can accurately pinpoint where to invest on further product design, giving them further confidence that they are making the most effective use of their resources.”