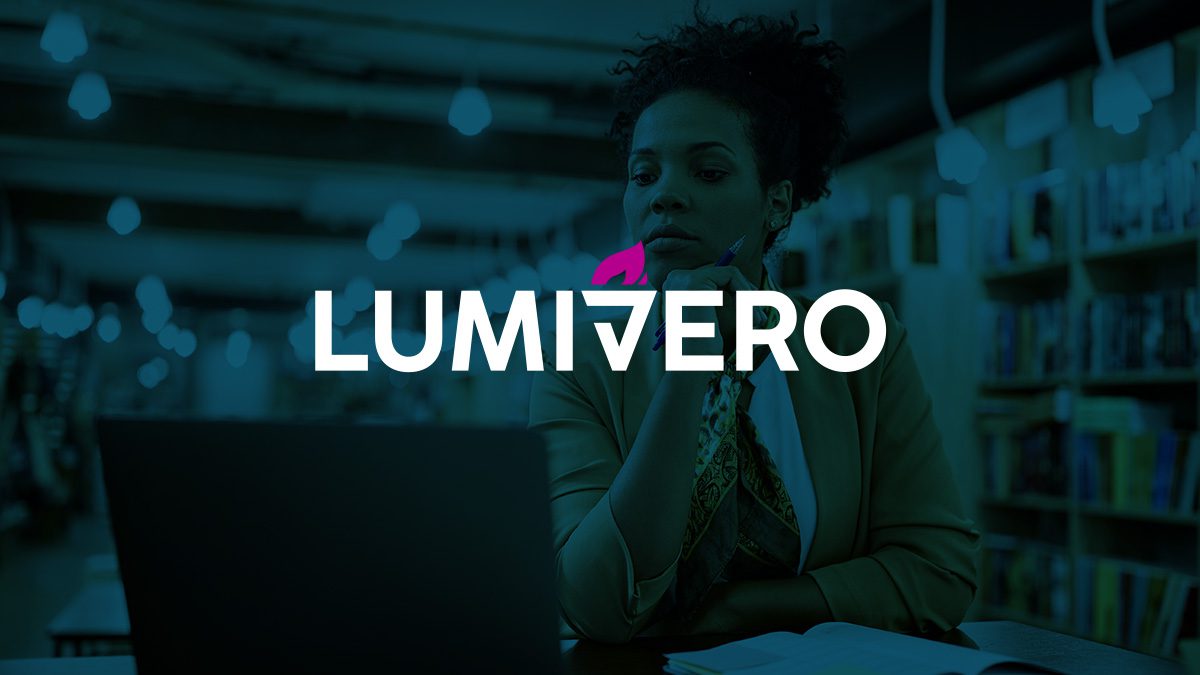
In Six Sigma analyses, there seems to be some low level confusion about Cpk and Ppk and what they actually represent. Very basically, Cpk is short term “noiseless” process capability where Ppk is long term “noisy” process capability. Some of the confusion regarding these two metrics may be because the automotive industry had at one time used Cpk to represent long term process capability and Ppk for short term, the complete opposite of the rest of the Six Sigma community. They have since conformed to the industry’s standard definitions. Another potential source of confusion is that Ppk is a much underutilized metric for what it measures. When developing a process performing at Six Sigma level, wouldn’t we ultimately want be focused on Ppk instead of Cpk? That is another subject that hopefully will receive more attention in the future.
Cpk can be used as a capability metric to provide insight on performance to a requirement if the process data used in the calculation comes from a normal distribution. If the process data is non-normal or it is the result of a combination of processes, then it provides an underestimation of the true non-conformance capability. You can evaluate the impact of the non-normality on Cpk by using Monte Carlo simulation in @RISK.