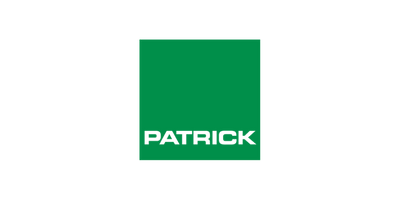
Patrick Engineering is a nationwide U.S. engineering, design, and project management firm with a long history of success on a variety of complex infrastructure projects. Clients include key government agencies, private and public utilities and FORTUNE 500 companies in a broad range of industries. Patrick focuses on providing concept planning, engineering, pre-construction services, procurement of materials and construction management of heavy infrastructure projects. This work is accomplished with technical experts in the fields of civil, structural, hydraulic, environmental, geotechnical, electrical engineering, relay and protection, geology, surveying, construction management, process control and GIS.
Patrick provides independent cost estimating, scheduling, and risk analysis services for the Massachusetts Bay Transportation Authority (MBTA) as the basis for budgeting and reserving funds for future requirements. @RISK software is used exclusively for program quantitative risk analysis. Estimates of cost and schedule duration are uncertain values, as the exact or discreet values are not known until complete. Given the inherent uncertainty of estimates, the best way to display them is with probability distributions of possible cost and schedule durations. The best application for this is statistical modelling, and Patrick uses @RISK software to assess cost and schedule contingency needs based on project or program risks.
Background
The Downtown Crossing Vertical Upgrade project was part of Massachusetts Bay Transportation Authority’s (MBTA) major elevator upgrade program to replace outdated and small elevators, as well as add new ones to meet accessibility requirements of the Americans with Disabilities Act. During design, several project risks were identified, such as subsurface conditions, pedestrian access and licensing agreements. According to Kim Kozak, Sr. Project Manager for Patrick Engineering, risk identification is just the first step in the determination of risk contingency. The development of the construction cost estimate and project schedule are the foundation of the risk model to which risks are linked. In addition to construction costs, other costs are factored, such as those attributed to client related costs and escalation.
“To do this, you need to work collaboratively with the client, with the designers, with the project management team, with anyone who will have insight into the project – you want them all involved,” explains Kozak. The full team for the Downtown Crossing station project included six organizations and approximately 20 team members, working with MBTA Project Controls led by Horace Cooper.
DKim Kozak
Project Manager, Patrick Engineering
Building a Collaborative Model
Patrick Engineering takes a unique approach to these types of complex projects: once they have the construction cost estimate and schedule, they hold a Quantitative Risk Workshop. This workshop is a collaborative brainstorming exercise that enables everyone involved to talk through specific elements of the project, as well as capture the impacts and probabilities of those impacts occurring. “We try to get people thinking, to encourage discussion, as even a small detail could lead to a giant risk,” said Kozak. “Similar to the situation with the Titanic – what seems like a minor detail could be enough to sink the entire ship.”
Through the Workshop process, the team is able to capture enough details to enable Patrick Engineering to build a risk model based on the minimum, most likely and maximum values, that provides the minimum and maximum value of those risk impacts, and assign appropriate levels of probability for those risks. The company uses @RISK software to assess project contingencies based on the cost and schedule risks, using Pert and Triangle distribution models. As each project has unique risks, the input for their models is determined on a per-project basis. This input can include:
- Designs risks, e.g. Is the completeness of design 100%? Can the project be constructed as designed?
- Schedule risks, e.g. complexity of the project, interaction with other projects
- Cost risks, e.g. If the construction date is pushed out, what are the risks associated with extended overhead costs for the contractor?
- Liquidated damages risks, e.g. If the property can’t be turned over on schedule, what are the associated risks for the contractor or client?
Kozak added, “Even if you’ve gone through the list of everything you can visualize on the drawings, there are still ‘unknown’ unknowns – you don’t know what you don’t know. So we included risks for the unknowns with the appropriate level of probability and impact as a percentage of schedule and cost elements for the Downtown Crossing Burnham Elevator project.”
While project contingency risks are typically captured as a percentage of total project costs, @RISK enables Patrick Engineering to assess contingency requirements at the appropriate level of risk. The software outputs provide them with a build-up of costs, including the level of accuracy of the estimate, as well as cost and schedule risks.